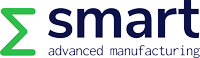
Gipuzkoa Science and Technology Park.
Paseo Mikeletegi, 59.
20009 San Sebastián. SPAIN
+34 943 309 009 – info@smarteureka.com
COORDINATOR
PARTNERS
RISE Research Institutes of Sweden AB
Promimic AB
Agaria AB
Fraunhofer IFAM
Tigres Gmbh
Download project leaflet: click here.
Gipuzkoa Science and Technology Park.
Paseo Mikeletegi, 59.
20009 San Sebastián. SPAIN
+34 943 309 009 – info@smarteureka.com