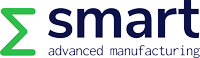
Gipuzkoa Science and Technology Park.
Paseo Mikeletegi, 59.
20009 San Sebastián. SPAIN
+34 943 309 009 – info@smarteureka.com
COORDINATOR
Turkish Aerospace Industry
The University of Sheffield, Advanced manufacturing research center
Aibuild
Additure
Prodigma
Voestalpine-Böhler
Gipuzkoa Science and Technology Park.
Paseo Mikeletegi, 59.
20009 San Sebastián. SPAIN
+34 943 309 009 – info@smarteureka.com